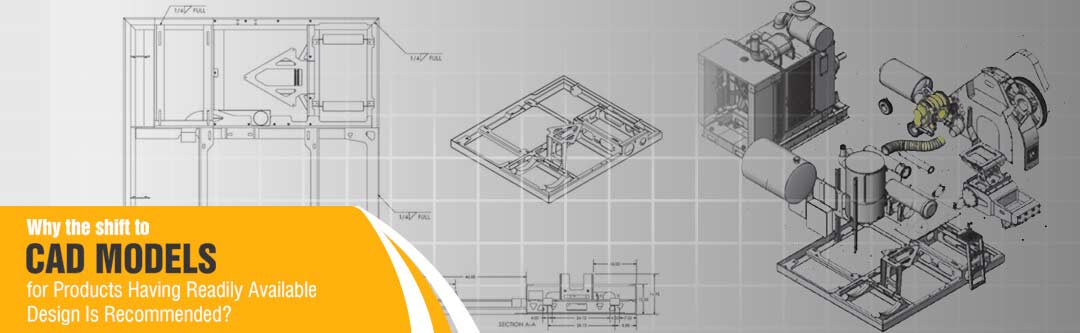
Working around CAD models is all it takes for a design engineer to convert the conceptualization of design to product development, bill of materials, manufacturing details and even for product lifecycle management (PLM). Designs to most of the products have been already been prepared, so what is left for todayโs design engineers is to enhance the features for betterment of safety and performance requirements.
In this era of technology, direct conversion of 2D drawings to CAD models is done extensively by most designers by scanning the existing pdf drawings through laser scanning techniques. The conversion is then simpler through several inbuilt functions of the software. However, the modeling technique demands a very high level of accuracy for appropriate design generation and hence the exact fabrication of new product.
Clientโs case study
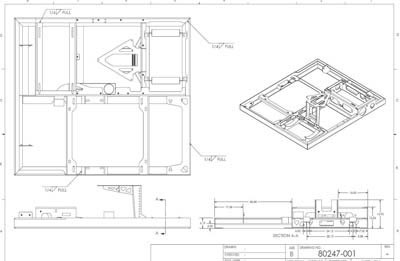
Many a times; digitization of design data becomes necessary for the ease in manufacturing and referencing for future modification in the designs. A road line equipment manufacturer in USA had to generate detailed assembly and fabrication drawings from PDFs and rough sketches.
These design details were studied by the engineers and were converted to individual component 3D models, assembly drawings and fabrication drawings with Bill of Materials (BOM). The final fabrication drawings contained all the manufacturing details, enabling the client to reduce the manufacturing time by almost 40%. Product development was significantly enhanced through the CAD conversion.
Comprehensive Design and efficient product development
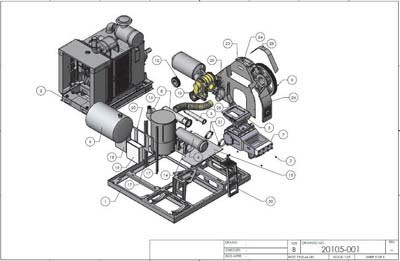
With advanced features and powerful tools for modeling incorporated in CAD software, assemblies can be created from conceptual sketches easily. Production ready assemblies can be made through the tools which will automatically generate Bill of Materials and costing documents, as the design evolves. Changes in design will correspond to updating of related information. The problems associated with 2D drawings in visualizing the product by investors and project stakeholders are eliminated by 3D CAD models. Inclusion of design detailing and better communication of design intent can be done with 3D CAD models, allowing changes in design features at early stages and strengthening development of the product.
Design automation and Customization for design optimization
Repetitive work related to designing and drafting is essentially eliminated through design automation and benefits the company for bid and large volume manufacturers. Infinite variations of models through a rule-based program will eliminate time-consuming process and easily generates models. Through customization tools, customization of parts is possible and features like painting or packaging can be added to the top-level of the assembly. SOLIDWORKS Part Catalogue allows creating several standard components, approved by manufacturers and stores it in the software, which can be retrieved as and when needed.
Manufacturing details
Manufacturing details like surface finish, tolerance, weldments etc. can be detailed in the assembly, there by generating one single assembly model for fabrication having Product Manufacturing Information โ PMI. Advanced CAD tools also allows generating prototypes of the product which can be tested in virtual environment for changes in design if need be. These assemblies can be further subjected to generate presentations and animations for end users. Assembly Cost Roll Up, a feature in SOLIDWORKS Premium only, rolls up the costs of all the components in the entire assembly. This helps in estimating total cost of assembly.
Conclusion
The case where even one of these benefits is non-existent, the phase of conceptualization to fabrication will turn into a much-disorganized process. Such haywire activities can never bear fruitful results with accuracy and quick product generation. Digitization of design through CAD models is the only way out for manufacturers and design engineers for optimized results.
Leave a Reply