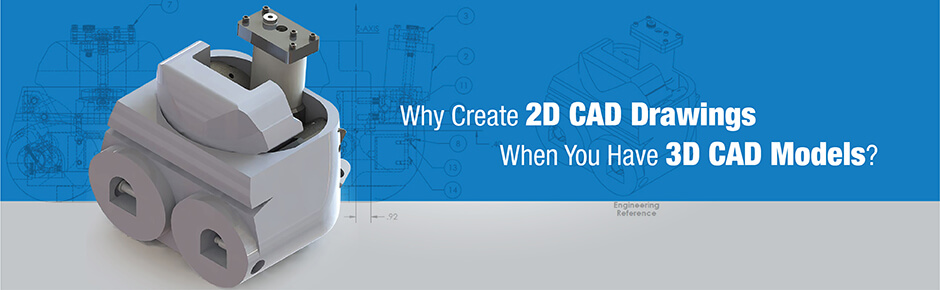
Table of Contents
2D CAD drawings have been with us since decades; they do this very important task of providing product manufacturing information to folks on the shop floor. These CAD drawings are the ultimate communication tools for engineers and are responsible for actual product manufacturing. Even when they look complex at times, we all love to decode the information out of the annotations that define the geometry.
But, there are few shortcomings of 2D CAD drawings which cannot be denied, when it comes to developing competitive products in a time bound situational market that we have today. 2D CAD drawings are time consuming to develop and often include errors that lead to production delay at some point of time. This leads to production wastage many times; in fact, it is estimated that 60% of the 2D CAD drawings do not match with their 3D counterparts, making it one of the prime reasons for wastage due to dimensional errors. Since every single thing of the design is flattened out in a sheet of paper, the chances of misinterpretations are evident.
How could you possibly remove these errors and save your organization from production wastage?
Design support partner for development of mechanical products ranging from industrial equipment, automotive components, machines and tools to building products, furniture and sheet metal components would work to your advantage. They primarily focus on delivering CAD and CAE solutions ranging from using Creo & SolidEdge for CAD conversion, AutoCAD 2D drawings & drafting, and SolidWorks 3D CAD modeling to FEA and CFD simulation to utilize design information efficiently and shorten the product development schedules.
MBD: New Approach to Tightly Integrate PMI with the Design
Model Based Design or also known as simply MBD is an interesting approach to eliminate the errors that we usually encounter when dealing with 2D drawings. The concept behind MBD is to eliminate the use of CAD drawings completely from the production process and instead focus on the 3D CAD model directly, with help of CAD designs. All the information about manufacturing processes is directly embedded onto the 3D model, making it more intelligent and useful for downstream applications in the shop floor.
What else could be the future of 3D modeling than MBD?
We use the 3D models mostly for marketing presentations and departmental level communication. But at the shop floor, we still rely on the drawings.
Giving the virtual model directly into the hands of a shop floor guy can improve design communication positively. You not only save yourself from developing manufacturing drawings from CAD models, but also reduce the chances of errors and misinterpretations due to enhanced visualization.
But this idea is lot more complex than it may appear, in case if youโre planning to integrate it with your existing manufacturing processes. If done correctly, benefits are in abundance; but it can go other way around and disturb your entire streamlined processes terribly. Organizations need a holistic approach and must align their people, process and product to enable MBD to work in their favor.
How to Get Started with MBD
Getting started with MBD takes time and requires a strategic approach to replace the 200 year old 2D drawings to CAD designs leading to 3D model-based processes- successfully. This begins with:
- People: For any idea or process to work positively within the organization, people always come first. The initiative has to drive from the management team i.e. top down approach rather than bottom-up since MBD considers different teams including manufacturing, operations, quality, purchasing, supply chain, support and so on. It is crucial to educate all these teams and establish a mindset first to become ready and accept the change.
- Process: One of the important parts of the implementation strategy is to focus on establishing the process seamlessly without much of the complexities. This can happen with using the MBD for smaller and simple projects first, rather than going for tough and bigger ones. With this approach, there are number of benefits; you learn about the mistakes, streamline the activities and establish best practices and upgrade infrastructure to prepare for the bigger projects.
- Product: For MBD to work effectively, you need to have the right CAD tools to represent the product manufacturing information accurately and easily. The tools must support the steps required in MBD in accordance with the ASME Y14.5 standards, such as 3D CAD design, 3D PMI definition, 3D PMI organization, 3D data sharing and template customization.
The Doโs and Donโts in MBD Implementation
There is an accurate summary of doโs and donโts available on SOLIDWORKS blog that you can follow. However, this is just a start and is far from a detailed implementation guide. It requires an in-depth analysis and practical customization as per specific manufacturing requirements. The points mentioned however, are pragmatic for most manufacturers today.
Key Aspects | DOs | DONTs |
---|---|---|
Key Aspects People |
DOs 1. Drive from top down 2. Establish a core implementation team 3. Motivate all involved |
DONTs 1. Donโt hesitate 2. Donโt take too big a bite at first 3. Donโt be confined to Design department alone |
Key Aspects Process |
DOs 4. Measure progress 5. Automate workflows 6. Update infrastructure |
DONTs 4. Donโt rely on 2D drawings as the master any more 5. Donโt send only 3D PDF to supply chain 6. Donโt overlook MBD over the web |
Key Aspects Product |
DOs 7. Penetrate with one or two manufacturing documents 8. Organize and present 3D PMI clearly 9. Customize and standardize templates 10. Validate models, PMI and derivatives |
DONTs 7. Donโt skip calling out critical to function 3D PMI 8. Donโt settle on graphical 3D PMI 9. Donโt exclude printouts 10. Donโt be limited by rudimentary 3D PDF |
Implementing MBD can be a challenging task for organizations that work with traditional manufacturing practices. It is difficult then for a manufacturer to streamline everything single handedly. This is where engineering design support services providers could be of help. Developing detailed information-rich 3D models and manufacturing documentation for pilot projects or a complete MBD implementation can be handled with a group of qualified resources at offshore centers rather than allocating in-house resources. This allows significant time to train in-house teams and update the infrastructure without affecting the production efficiency.
Leave a Reply