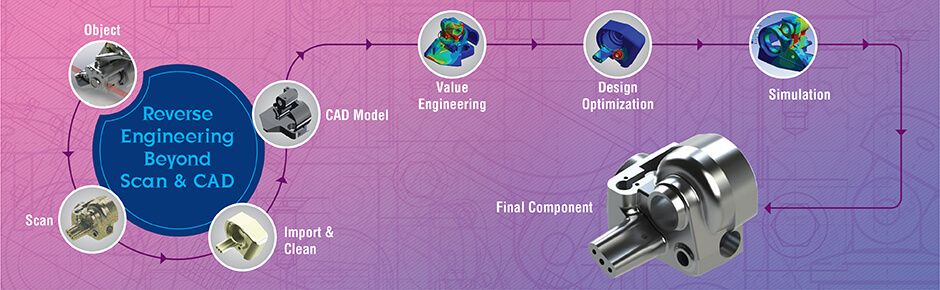
Table of Contents
The manufacturing industry has been long established with sophisticated machinery setups even before the times of CAD, and they have been operational to deliver optimum results. But simultaneously, factory/plant owners and design engineers have made changes, replacements, realignments and upgradation to parts owing to continuous operational wear and tear.
Now, as these machines were built pre-CAD era, their designs were never digitized and neither were the changes. The original fabrication drawings, assembly drawings and part models also made on typical engineering drawing sheets have also degraded. And it is almost impossible to have every maintenance and realignment documented when designs are on paper, especially when the equipment is operated by multiple operators, engineers, and OEMs.
The big challenge of productivity
With so many alterations and drawings or drafts available on paper that is not in sync with the as-built set-up, decision making for replacement or re-engineering is hindered. Most manufacturers follow the thumb rules (which can never be accurate or efficient) merely based on hunches, out of ordinary behavior/output of the machine, component or part, assembly line etc. and in some cases production variation and increased downtimes.
But the issue of challenges does not stop here; it goes beyond. When decision-making process is not backed by significant design knowledge it is always clouded by a fear of how the replacement will fit in. It not only leads to machine/assembly line idle time but also the inability to decide as to which part exactly needs upgradation.
When decisions are to be made for critical machine part or a critical section of the assembly line, manufacturers or the plant owner would not want to take the risk of catastrophic damages. Consequently, they resort to reverse engineering and understand the existing conditions, re-engineer and replace the part.
To avoid such incidents, most named manufacturers plan the downtime for regular maintenance to ensure the smooth functioning of their production lines. Recently, in April of 2018, Tesla motors announced a planned downtime of Model 3 electric car to improve automation and systematically address bottlenecks to increase production rates.
If these downtimes are not planned for maintenance and replace or re-engineer the critical part, any machine in the assembly line might fail anytime and may result in loss of millions of dollars to the manufacturing company.
Evaluating the concurrency of reverse engineering
However, being in the manufacturing industry for years, OEMs and plant owners know that such ill fate may come any time even with reverse engineering. Failures have occurred in the past and results have been devastating (in terms of monetary losses as well as brand identity in the market) to the company.
Such planned maintenance and downtimes will serve the purpose of inspecting and re-evaluating the production plant capacity and enhance the delivery quality. However, reverse engineering sometimes creates challenges with manufacturersโ fabrication facility and the tooling capacity to recreate identical parts.
Solving reverse engineering challenges with design analysis
There is a popular argument that reverse engineering followed by design analysis and simulation essentially solves the challenges of design incompatibility, part suitability, and operational performance.
However, mere CAD modeling from scanned data and simulation of those models wonโt help when the parts have become obsolete and need to fill up the void in design formation with technology upgradations.
For example, when there has to be a design change in terms of ergonomics factor and also the economy of the product is to be considered under the light of competitorsโ product, it takes studying the actual source code of the design formation and optimizing that very code in order to optimize the features and hence the price.
This is to say that reverse engineering should essentially be accompanied with fundamental design changes with value-added engineering solutions to keep up with the pricing as well as evolving ergonomics.
Forward thinking with reverse engineering
To sum up the aforementioned example, reverse engineering is not just about scanning and modeling to retrieve design intelligence so that the obsolete part can be replicated; it goes a step forward. The entire idea of reverse engineering actually has close ties with design upgradation, value engineering and digitizing the designs for future reference.
In fact, it extends to the length of setting up entire product lifecycle by implementing PDM and vault creation. Documenting every change in the CAD model whenever there is an update in the physical part will make the decision-making process more efficient and not clouded by any preconceived ideas or events.
Leave a Reply