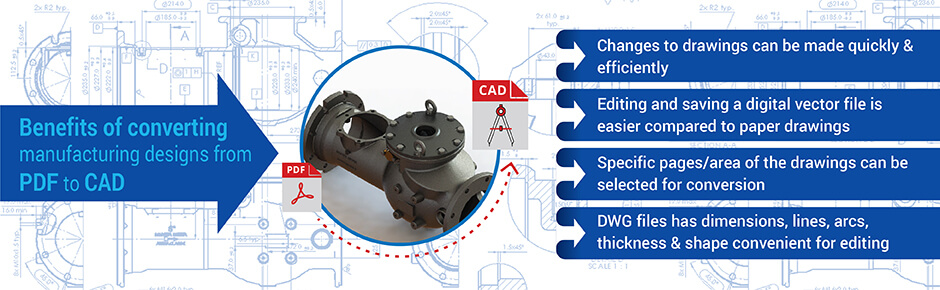
Table of Contents
Irrespective of the industrial segments, or even the familiarity of the file formats, you as a professional design engineer have encountered PDFs at several points. The most popular file format โ PDFs โ remains a perfect way to share data and exchange information. Especially for data as critical as a machine component drawing, part drawing, assembly model, PDFs are a popular choice for design data exchange.
However, along with PDF, CAD software too forms an inseparable entity for industrial design engineers as well as manufacturing companies. And this can be problematic if you want to use PDF with CAD. The alternative is converting PDF to CAD for making the most of designs. Typically, a PDF drawing or a 2D drafting on paper is scanned and imported to a suitable CAD platform for making the mechanical drawings or technical manufacturing drafting available in editable DWG or other standard CAD format.
Why is PDFs so popular?
PDF – an abbreviation of Portable Document Format โ is a file that can be transferred from one device to another without significant challenges of data distortion and seamlessly exchange across different software entities. Another interesting fact about PDF it supports both raster and vector elements.
But for CAD engineers and managers working with PDF and CAD platforms is a big challenge since editing PDF is incredibly difficult. And thus, design professionals in industrial designing and building construction designing find it challenging to work with PDF.
Engineering drawings and designs pass through multiple design revisions. Mark-up drawings, changes by various project stakeholders, and client feedbacks form the prime reasons for design changes. And hence CAD engineers need to convert paper based drawings to CAD formats using PDF to CAD converters.
Changing PDF to CAD
The phrase essentially means transforming the design data from PDF to CAD models using a suitable CAD platform like AutoCAD. Usually a 2D drawing or 2D drafting in CAD software will be saved as a DXF or DWG file format in AutoCAD โ native CAD file formats. Furthermore, a typical DWG file will support both 2D and 3D geometry which gives an ease to the design engineer to edit and modify the designs based on a 360 degree view of the component or an entire machine.
On the other hand, DXF files, has an advantage is that it is an open standard format. It means that a CAD file created in AutoCAD can be exported to SolidWorks can be viewed and edited there. It is a kind of universal file and ideal solution for manufacturing companies. It so because manufacturers often outsource part of CAD modeling of major designs to offshore companies to gain on costs charged at hourly rates and expertise. In such situations, DXF files work the best.
It is almost impressible to find an error message saying โfile incompatibleโ or โfile format not supportedโ for almost any CAD platform.
But, a drawback of DXF file the same CAD file saved in DXF format will occupy higher disk space as compared to DWG file as the latter is a binary type. Secondly, it also does not support some of the CAD elements like dynamic blocks and some data is lost.
How do you transform PDF to CAD?
There are far too many companies that transform PDF paper based drawings into CAD files by scanning as well as by manual tracing. As the name suggests, the drafters at the CAD design support service provider company will import PDF to CAD platform and trace all over the geometrical designs of the component, machine, assembly, sheet metal part, etc.
This CAD conversion method has a benefit of human understanding like the AutoCAD drafter will exactly know which part of the design is being transformed and changes whatsoever can be incorporated easily. Ideally, this type of CAD conversion process is so precise that one can say it transform entire PDF to CAD lines and angles. However, it has a disadvantage that manual tracing gets time consuming which is not affordable to manufacturers in order to meet scheduling of dispatch and final product delivery.
Alternatively, there is an option for automatic tracing of PDF design information using third party software that scans the PDF and when imported to CAD interface will convert the entire file into a vector file format compatible to native CAD like DXF or DWG. Edges, angles, bends, embossing etc. can be detected separately and redrawn as vector entities in CAD. It essentially transforms raster to Vector that one can say it is technically equivalent to raster to vector conversion.
Other available options for PDF to CAD conversion
Other option to convert any PDFs to a CAD file is using an online converter that does the job reasonably well. But such methods are only used for conversions that do not need precision or accuracy. Online PDF to CAD converters are very quick and very efficient in converting the files to native CAD formats, but they cannot offer the same high quality outputs as in case of manual or automatic tracing.
Online CAD converter software or platforms are dedicated to raster to vector conversion and hence, they arenโt particularly for PDF to CAD conversion.
Second disadvantage of using an online CAD converter is that it generally comes with a strict permissible limitation file sizes. They need a limited file size upload and allows only up to a limited number of conversion for a particular user/login. And above all else, when a design engineer or a manufacturing company is putting their designs online they are out in the open exposed to all kinds of security risks.
Benefits of converting PDF to CAD
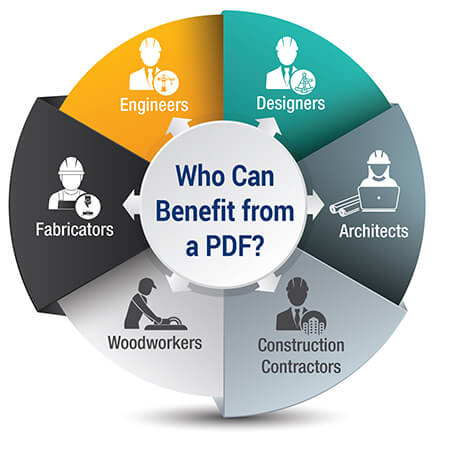
With manual or automatic tracing methods, design engineers and CAD drafters are easily able to convert raster as well as vector elements of PDF files to CAD file. Vectors, ORC, lines etc. all can be transformed to equivalent and suitable CAD data.
Another advantage is, in contrast to other online converters, an automatic converter treats all the small images as single entity sparing the user from reassembling the PDF intelligence post conversion. Saving CAD arcs and circles are made up of lines instead of curves which cannot be saved by a PDF. Hence by converting the file to CAD, they can essentially be edited and interpreted more objectively.
Furthermore, for mechanical component designs, each line type has its own significance โ such as hatch pattern, dotted line, center line etc. Suitable CAD converter will ensure that this significance is maintained by stressing over line thickness, origin, pattern etc. by transforming the data into DXF file format.
Final word
With these arguments, methods and benefits discussed above, it is apparent that PDF isolates the drawings and mechanical designs once made. They do not give flexibility to designers for upgrading; while, CAD, on the other hand, does. Manufacturing companies and fabrication firms thus can keep their design data in a digitized format and can upgrade them as and when needed.
Converting PDF to CAD or DWG/DXF is the only way to save vectorized design data according to the need of the shop floor and other downstream engineering needs.
Leave a Reply