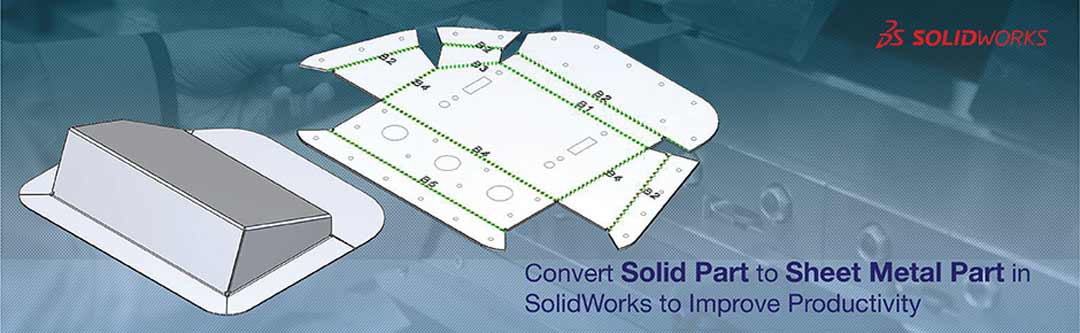
SolidWorks sheet metal design capability makes manufacturers within the sheet metal product industry to easily derive flat patterns with required gauge and bend allowances quickly. It is because of these friendly features that makes SolidWorks as one of the leading choices for engineers across the globe.
Making a sheet metal part is although quick, there may be instances when the 3D CAD modeling might be started as a solid and then the requirement would be of converting the solid to a sheet metal part. The major difference between a sheet metal and solid part is that for sheet metal, the part is formed from a flat sheet as compared to solid where the part is formed by removing material from a solid piece of metal. CAD specialists also prefer to develop a part through solid or surface models for difficult sheet metal designs and then convert it into a sheet metal flat pattern.
SolidWorks offers a great feature called โConvert to Sheet Metalโ to help convert solid part to a sheet metal component which can then be flattened and utilized for shop floor requirements. With this feature, a solid object can be easily converted to a sheet metal part with required gauge, k-factor and bend allowances. After the conversion, one can easily extract flat pattern drawings and fabrication for part manufacturing requirements.
To convert the solid part:
Create the solid part using the solid modeling tools. The example shown here is easy for solid modeling. For creating a sheet metal part however, it would require calculating angles, repeating bends, custom end flanges, etc.
Click on the Convert to Sheet Metal button or go to Insert > Sheet Metal > Convert to Sheet Metal.
In the property manager, under Sheet Metal Gauges, select the gauge table to use from the existing library or upload your own.
The next step is to change the sheet metal parameters by first selecting a fixed face of the part. Next, select the sheet thickness and default bend radius.
Now, select the edges of the model that will form bends using Bend Edges. Selecting the edges will display callouts for each edge where you can specify the bend radii and rip gaps for each edge separately.
Now, set the bend allowance type and value for each bend using Custom Bend Allowance option. To add relief cuts for the inserted bends, select the type of relief cut, i.e. Rectangular, Tear or Obround.
Click on flatten button on the sheet metal toolbar to flatten the part consisting of specified bends and rips.
SolidWorks sheet metal modeling is quick and easy. However, for complex components that require specifying details to accurately create a sheet metal model, utilizing this trick to first develop a solid model and then convert to a sheet metal model is extremely useful. Apart from increasing the productivity, the chances of errors and design changes reduces considerably. The designer does not have to worry about allowances and angles during the initial design process.
Images Source: help.solidworks.com
Leave a Reply